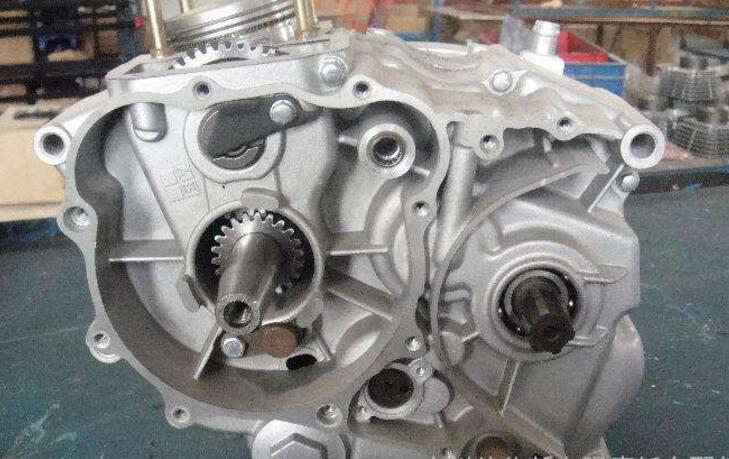
概述
鋁合金壓鑄件在制造業(yè)的運(yùn)用已趨于成熟,并得到廣泛的運(yùn)用,以摩托車為例,諸如:輪轂、汽缸頭、缸體、曲軸箱、活塞、曲軸箱蓋等均已完成鋁合金化。摩托車曲軸箱鋁合金壓鑄是通過高速、高壓將鋁合金溶液高速壓入?yún)⒄债a(chǎn)品圖紙?jiān)O(shè)計(jì)開制的模具型腔內(nèi),并施以保壓凝固成型,再脫模取出。在該過程中基于鑄造工程參數(shù)的控制實(shí)現(xiàn)整個(gè)過程的穩(wěn)定性及過程控制。
鋁合金壓鑄件具有質(zhì)量輕、性能好、生產(chǎn)效率高、表面質(zhì)量好、尺寸精度高等諸多優(yōu)點(diǎn)。但在實(shí)際生產(chǎn)中出現(xiàn)的品質(zhì)問題也十分突出,如花紋、流痕、冷隔、充型不良、夾渣、壓檢不良、氣泡、多肉、裂紋、欠鑄、燒蝕、粘模、氣縮孔、飛皮等,缺陷形成有多方面的原因,必須找到問題出現(xiàn)的原因才能作出正確的判斷,才能提出有效、可行的改善對(duì)策。
本文主要以摩托車曲軸箱壓鑄件加工過程中出現(xiàn)的壓檢不良現(xiàn)象為研究對(duì)象,針對(duì)其壓鑄過程中可能造成的原因進(jìn)行分析尋求解決對(duì)策。
1、 壓檢不良
壓檢是在箱體加工完成后對(duì)油道部分進(jìn)行氣密性檢查的工序過程。壓檢原理:是指在氣密性檢查時(shí),空氣填充過油區(qū)域,通過對(duì)比輸入壓力與反饋壓力的差值進(jìn)行氣密性判斷。區(qū)域存在空氣泄漏時(shí),致使反饋的壓力與輸入壓力存在差值,當(dāng)差值超過規(guī)定范圍值時(shí)報(bào)警燈亮起,反映出工件壓檢不良,需對(duì)工件進(jìn)行水檢查找漏點(diǎn),能發(fā)現(xiàn)漏點(diǎn)的工件需區(qū)分并報(bào)廢處理。
針對(duì)我公司生產(chǎn)的125型曲軸箱1壓檢工程如圖1所示,壓檢區(qū)域如圖2所示部分,壓檢不良確認(rèn)的漏點(diǎn)如圖3所示,且該種箱體漏點(diǎn)均是同位置。
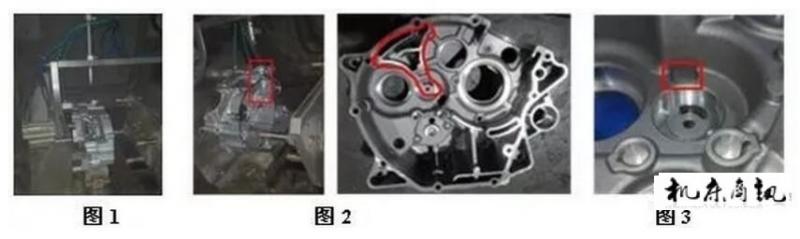
1.1壓檢不良的影響
壓檢不良比例約為15%,不僅對(duì)品質(zhì)有影響也對(duì)生產(chǎn)工時(shí)有影響。
1.1.1壓檢不良影響品質(zhì)
壓檢不良就是反應(yīng)箱體油道內(nèi)存在非正常泄漏點(diǎn),在正常工作時(shí)機(jī)油對(duì)發(fā)動(dòng)機(jī)進(jìn)行潤(rùn)滑,油道就是定向滿足機(jī)油對(duì)各需要潤(rùn)滑部位進(jìn)行潤(rùn)滑。若存在小漏點(diǎn)因壓力損失遠(yuǎn)小于機(jī)油泵輸出的壓力,不會(huì)造成發(fā)動(dòng)機(jī)異常,但會(huì)引起機(jī)油發(fā)泡;若存在足夠大的泄漏點(diǎn),會(huì)嚴(yán)重?fù)p失油壓致使機(jī)油無(wú)法達(dá)到缸頭、缸體進(jìn)行潤(rùn)滑,可能造成發(fā)動(dòng)機(jī)拉缸,從而停止工作,帶來(lái)安全隱患。
1.1.2壓檢不良影響工時(shí)
當(dāng)壓檢不良指示燈亮起時(shí),壓檢夾具連同工件會(huì)自動(dòng)沉水檢查漏點(diǎn)。每次沉水檢漏過程需平均耗時(shí)30S,當(dāng)沉水比例較大時(shí),是無(wú)法完成正常生產(chǎn)計(jì)劃的。
2、壓檢不良現(xiàn)象原因分類
壓檢過程主要涉及三部分:工件、夾具、氣源控制系統(tǒng),出現(xiàn)壓檢不良需要分三方面對(duì)其進(jìn)行檢查、確認(rèn)。
2.1氣源控制系統(tǒng)
生產(chǎn)線氣源控制系統(tǒng)是一定的,通用于生產(chǎn)所有型號(hào)箱體的壓檢過程,在生產(chǎn)其他箱體時(shí)未出現(xiàn)壓檢異常,且設(shè)備維修組對(duì)其進(jìn)行點(diǎn)檢確認(rèn)無(wú)異常,從而排除氣源控制系統(tǒng)異常直接引起壓檢不良。
2.2壓檢夾具
壓檢不良就夾具而言,當(dāng)其封堵不嚴(yán)密時(shí)會(huì)自然泄氣造成壓檢不良,確認(rèn)現(xiàn)象時(shí)對(duì)夾具進(jìn)行密封墊全套更換以排除破損、變形造成不良。另外,針對(duì)夾具專門制作了125型曲軸箱1的壓檢標(biāo)準(zhǔn)樣件,用于在生產(chǎn)時(shí)對(duì)夾具進(jìn)行有效性確認(rèn),可以排除夾具造成壓檢不良現(xiàn)象。
2.3加工件
排除氣源控制系統(tǒng)、夾具等因素,明確壓檢不良是來(lái)至于工件本身。
3、產(chǎn)生原因分析
目視確認(rèn)漏點(diǎn)位于非加工面上,應(yīng)為鑄造過程出現(xiàn)的缺陷問題。由于水檢現(xiàn)象時(shí)連續(xù)的圓形水泡(若為穿透性裂紋水檢現(xiàn)象因?yàn)榉兴瓭L狀),且作色滲透檢查無(wú)線形作色劑殘留,可排除該處不良是穿透性裂紋引起。從鑄造工藝調(diào)整方面入手,以 4M為基礎(chǔ)進(jìn)行壓檢不良原因的分析。
3.1鋁材成分
鋁液成分異常可引起凝固組織疏松,另外含渣、含氣量大亦可能形成渣孔、氣孔,造成凝固后組織不致密。檢測(cè)鋁材成分如下表1:

實(shí)際鋁液除渣操作按工藝要求執(zhí)行,除渣周期為1次/2小時(shí),且造渣劑(除渣、除氣混合劑)與鋁液比例按0.3%投放進(jìn)行除渣、除氣。該工藝通用于所有箱體制造生產(chǎn),而其他車型箱體無(wú)壓檢不良,側(cè)面證明非鋁材原因造成壓檢不良現(xiàn)象。
3 .2鑄造壓力
鑄造過程中鑄造壓力不足時(shí),鑄件致密程度受影響,鋁液的膨脹性很大,壓力不足時(shí)有足夠的區(qū)域與時(shí)間形核并長(zhǎng)成枝晶狀,而在晶界面凝固收縮就會(huì)形成疏松,尤其是在非直接壓力方向上,通過后續(xù)的保壓是改變不了組織形態(tài)的。在后工序加工后壓檢時(shí)會(huì)因組織疏松形成泄漏。
3 .2.1壓力改善及效果
正常生產(chǎn)時(shí)鑄造壓力為640±20Kg/cm2,分別調(diào)整為600 Kg/cm2、700Kg/cm2、730Kg/cm2進(jìn)行生產(chǎn)試驗(yàn),試驗(yàn)數(shù)量為各20件,直接進(jìn)行加工確認(rèn)壓檢不良比例,結(jié)果為:600 Kg/cm2試樣不良6件,占比30%,另外,鑄件遠(yuǎn)端表面存在冷隔、褶皺,影響鑄件外觀;700Kg/cm2試樣不良7件,占比35%;730Kg/cm2試樣不良11件,占比55%。驗(yàn)證結(jié)果:壓力改善對(duì)鑄件壓檢不良無(wú)改善效果。
3 .3鑄造速度
鑄造速度分:第一階段速度、第二階段速度。第一階段速度過高,在壓射過程會(huì)形成卷氣進(jìn)入鋁液,并最終分散在鑄件內(nèi)部形成氣孔;第一階段速度過低,會(huì)降低鋁液溫度、降低鋁液的流動(dòng)性,開始形成晶核并長(zhǎng)大,在后期的高速壓射時(shí)已無(wú)法均勻形核,較大的晶核會(huì)造成鑄件斷面質(zhì)點(diǎn)粗大不均勻,夾渣、夾氣后內(nèi)部組織不致密。第二階段速度過低,導(dǎo)致澆口速度不足,鋁液以流狀進(jìn)入充填,沖填時(shí)間過慢,形核長(zhǎng)大造成組織粗大[2]。實(shí)際高速為2.5-2.8m/s,不會(huì)出現(xiàn)速度過高情況。
3 .3.1速度改善及效果
低速度為0.15±0.05m/s,處在相對(duì)較小值范圍,本次驗(yàn)證未對(duì)其進(jìn)行降速試驗(yàn)。將第二階段速度提高至3.0m/s、3.2 m/s,分別試作20件試樣進(jìn)行壓檢確認(rèn),不良比例分別為25%、15%,對(duì)壓檢不良沒有改善效果。
3 .4沖頭潤(rùn)滑油
沖頭油在壓鑄過程中對(duì)活塞與料筒進(jìn)行潤(rùn)滑,當(dāng)沖頭油滴在料筒時(shí),注入鋁液會(huì)起明火燃燒,產(chǎn)生氣體。當(dāng)前正常生產(chǎn)狀態(tài)中沖頭油滴注在沖頭上方,在沖頭運(yùn)行中進(jìn)行潤(rùn)滑,但在連續(xù)生產(chǎn)中沖頭潤(rùn)滑油仍會(huì)積累,在注入鋁液時(shí)明火燃燒,產(chǎn)生氣體進(jìn)入型腔,增加鑄件內(nèi)部氣孔含量。
3 .4.1沖頭潤(rùn)滑油改善及效果
為了減少潤(rùn)滑油的積累并更均勻的潤(rùn)滑料筒內(nèi)壁,采用噴霧方式供給潤(rùn)滑油并將單次油量降低至3ml。試驗(yàn)20件,加工壓檢不良數(shù)為5件,不良占比25%。沖頭潤(rùn)滑油供給方式改變及油量下降對(duì)壓檢不良無(wú)改善效果。
3.5鋁液溫度
生產(chǎn)中鋁液溫度對(duì)鑄造影響十分重大,當(dāng)鋁液溫度過低時(shí),鑄件成型不夠充分,在結(jié)構(gòu)復(fù)雜及薄壁處體現(xiàn)尤為明顯;當(dāng)鋁液溫度過高時(shí),凝固時(shí)間延長(zhǎng),同時(shí)模具溫度升高,致使在肉厚及熱結(jié)部位最后凝固。從曲軸箱壓檢不良漏點(diǎn)來(lái)看,該處正處于熱結(jié)區(qū)域。
3 .5.1鋁液溫度降低及效果
原始鑄造鋁液溫度為675±15℃,當(dāng)溫度處在下限時(shí),壓檢不良仍然出現(xiàn)。驗(yàn)證時(shí)設(shè)置鋁液溫度為640℃,試作試樣20件,不良數(shù)量為3件,占比15%。結(jié)論:以降低鋁液溫度來(lái)改善該處壓檢不良效果不明顯。
3.6 模具溫度
模具溫度涉及三方面(模具冷卻水、離型劑吹附、鋁液溫度)的影響。在上述3.5中已排除了鋁液溫度的影響。如模具冷卻水出現(xiàn)堵塞,會(huì)導(dǎo)致局部溫度異常升高,僅靠離型劑降溫是遠(yuǎn)遠(yuǎn)不夠的,此時(shí)鑄件該位置處為最后凝固區(qū)域,可能出現(xiàn)氣縮孔。如離型劑吹附不均勻或量不足時(shí),會(huì)出現(xiàn)鑄件拉模及燒附粘鋁,破壞鑄件表面硬質(zhì)層,當(dāng)另一硬質(zhì)層面被加工時(shí),極易出現(xiàn)壓檢漏氣。
3 .6.1模具溫度改善及效果
(1)檢查確認(rèn)模具冷卻水均無(wú)堵塞,且與其他機(jī)種模具流量近似;(2)對(duì)應(yīng)鑄件壓檢不良的型腔區(qū)域,增加離型劑銅管吹附數(shù)量(1-2支),模溫測(cè)量如圖5所示,試作樣件30件(離型劑量大模溫上升緩慢),出現(xiàn)壓檢不良4件;延長(zhǎng)1-1.5s吹附時(shí)間,試作樣件表面冷隔嚴(yán)重,未作壓檢工序驗(yàn)證。
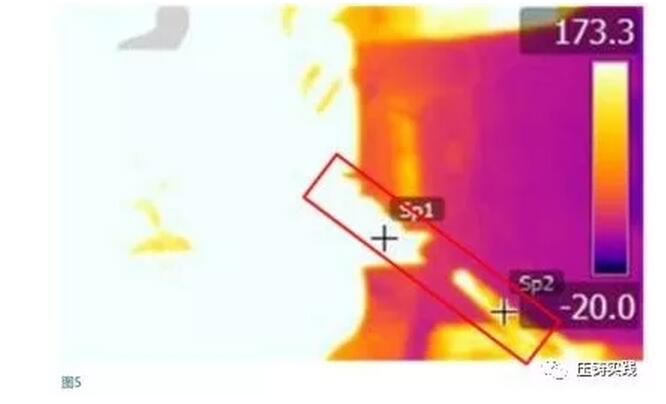
3.7 鑄造工藝調(diào)整總結(jié)
對(duì)鑄造過程中多個(gè)能造成鑄件壓檢不良的重要因素進(jìn)行原因分析及改善試驗(yàn),均無(wú)明顯改善效果。從鑄造理論而言,上述影響因素的調(diào)整應(yīng)取得一定效果,實(shí)際情況則表明在大的范圍里,上述因素的調(diào)整帶來(lái)的效果可能微乎其微。在工藝驗(yàn)證的基礎(chǔ)上,進(jìn)而展開對(duì)產(chǎn)品結(jié)構(gòu)及制造模具的檢討,以尋找到有效改善的對(duì)策。
4、加工余量
由于鑄造品尺寸精度較低而且存在收縮性,一般收縮率為5/1000,為了滿足裝配性等尺寸精度要求,在設(shè)計(jì)模具時(shí)在產(chǎn)品具有裝配、精度要求高的局部增加加工余量,再通過加工去掉余量,得到符合要求的尺寸精度。
4.1 加工余量確認(rèn)
對(duì)比加工完成品及毛坯實(shí)物,油道路徑LD68孔(如圖6)是需要加工來(lái)保證尺寸。在漏點(diǎn)部位(如圖7)解剖兩種狀態(tài)部品作截面尺寸對(duì)比如下圖8、圖9,確認(rèn)遠(yuǎn)端孔加工單邊余量為2.5mm左右。這與壓鑄中毛坯加工余量《1mm相悖。確認(rèn)圖紙?jiān)O(shè)計(jì)孔的加工余量為單邊0.75mm,由于該孔長(zhǎng)度為102mm、拔模斜度為1.5°,導(dǎo)致上述LD68孔加工余量過大情況。壓鑄件存在氣孔,加工余量過大會(huì)使內(nèi)部氣縮孔暴露,LD68孔油道壓檢不良與之可能存在相關(guān)聯(lián)系。
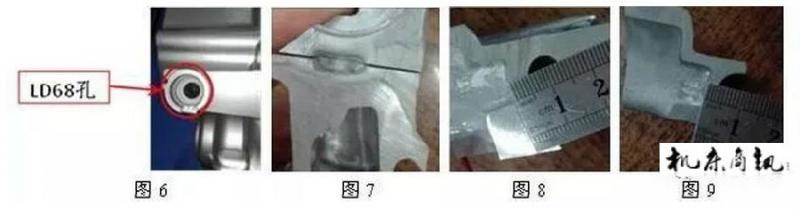
4.2 加工余量改善及效果
改善方案:減小LD68孔加工余量。根據(jù)毛坯圖紙LD68孔尺寸,孔深度是有裝配關(guān)系要求的,在考慮拔模能力時(shí),將型芯拔模斜度減小至1°,可將遠(yuǎn)端單邊加工余量減小0.85mm,盡可能避免內(nèi)部氣孔暴露。
將拔模斜度為1.5°的型芯更換為拔模斜度為1°型芯,生產(chǎn)工藝條件正常設(shè)置,試生產(chǎn)40件,無(wú)壓檢不良出現(xiàn)。為了確認(rèn)改善效果的穩(wěn)定性,進(jìn)行了批量驗(yàn)證,生產(chǎn)中無(wú)異常情況出現(xiàn),該處漏點(diǎn)亦無(wú)壓檢不良出現(xiàn)。
5、 結(jié)束語(yǔ)
壓鑄件加工后出現(xiàn)壓檢不良問題是較為常見的現(xiàn)象,有時(shí)候調(diào)整工藝參數(shù)是能解決的,但并不是都靠工藝參數(shù)能解決。具體問題需要具體分析,找到本質(zhì)的原因才能直接、有效的對(duì)策。該125型曲軸箱1壓檢不良,經(jīng)驗(yàn)證得出是因?yàn)檩^大的加工余量致使熱結(jié)部分氣縮孔暴露,與非加工面出現(xiàn)粘模現(xiàn)象同時(shí)發(fā)生,產(chǎn)生的漏氣現(xiàn)象。經(jīng)過改善減小加工余量,提高加工面的致密度,可消除壓檢不良。當(dāng)然,不同產(chǎn)品、不同結(jié)構(gòu)處的壓檢不良應(yīng)具體分析,尋找切合實(shí)際的解決方案。
本文作者:重慶建設(shè)·雅馬哈摩托車有限公司 鑄造技術(shù)部 羅久林、唐和雍